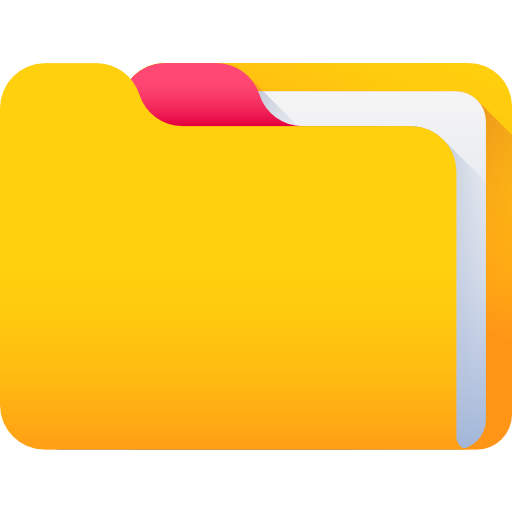
Global Refractory Bricks Market
Pages:
189
Date:
28 June 2024
Industry:
Construction and Manufacturing
Global Refractory Bricks Market, which are also called fire bricks, are bricks specially designed and manufactured to handle intense heat and challenging industrial environments. The starting materials for these types of bricks are the stuff comprising alumina, silica, magnesia, and several other refractory minerals, which endow them with the property of having high heat resistance and thermal stability. Tough refractory bricks are crucially applied for lining machinery in steel works, stoves, cement and other chemical processing that keep machines from extreme thermal breaks and wear. The fact that it cannot only withstand high temperatures but also guarantee structural integrity and thermal insulation adds to their versatility and makes them the primary components in most industrial processes. Refractory bricks of different sizes and shapes with concentrations of different compositions are designed specifically for different applications, and their good performance is the guarantees of the fire prevention, safety, and reliable operation of a high-temperature operating environment. The Asia-Pacific region, in particular, China, assuming the leading role in the global refractory bricks market, commands the most significant position in this market. China is pre-eminent due to its enormous industrial sector, especially because of the startling figures in the nickelates (substances such as zirconia and silicon carbide) for cement production or various kinds of refractory materials used by steel makers.
Player Names
- ArcelorMittal Refractories (Luxembourg)
- Colonial Manufacturing (United States)
- Darley Firebrick (United States)
- R. Refractory (China)
- Kelsen (China)
- Kilnlinings (United States)
- Melbourne Fire Brick Company (Australia)
- Qinghua Refractories (China)
- Rath (Austria)
- Refratechnik (Germany)
- RHI Magnesita (Austria)
- ThermaGlo (United States)
- TRL Krosaki (India)
- Vitcas (United Kingdom)
Segment Analysis
1. By Product Type
- Shaped
- Unshaped
2. By Application
- Metallurgy
- Furnaces
- Kilns
- Incinerators
- Others
Market Drivers
The refractory bricks are absolutely critical materials in the industries including cement, steel, ceramics, glass, petrochemicals, and non-ferrous metals. The increasing of these industries, which are pushed by factors such as urbanization, transport infrastructure development and industrialization, have directly caused the almost constant increase of refractory bricks demand. Steel Industry Demand: The steels consume most refractory bricks from the steel industry. The steel demand will get higher as the world is industrializing with infrastructural development, passenger and mass vehicles and due to the ongoing construction projects, which will result to making the use of refractory bricks for lining furnaces, converters, ladles and other steel making equipment that will proportionally rise this demand. The cement production is also a big user of refractory bricks that are primarily used in kilns and furnace of virtually any manufacturing process for cement. The construction industry is seen as a market with steady growth all around the world, accompanied by growing urbanization trends and infrastructure programs that ensure a good demand for cement. Hence, a good demand for refractory bricks is also guaranteed.
Market Trends
The industrial sector is increasingly moving towards energy efficiency and sustainability. Due to their properties that prevent heat transfer, refractory bricks are used on walls and ceilings of a furnace so that industries can effectively lower the energy consumption and cut greenhouse gas emissions. Eco-friendly product development and refractory processes might be supported by such market trends, so this might be the competitive edge of manufacturers. The refractory branch is experiencing a sequence of the research and development process that is supposed to improve both the performance and the durability of refractory bricks. Among the materials used in the production of refractory linings are alumina, silicon carbide, and zirconia. Presently, these advanced materials are able to survive higher temperatures, corrosive environments, and mechanical stress making them more reliable than the more common alternatives. It becomes compared to the bricks formed traditionally, the bricks with monolithic shape are less widely used but these are in very high demand. This is because of the installation ease and the lower downtime for an ordinary maintenance coupled with the better refractory performance. Companies manufacturing uniform, tailored to certain producers’ operations solutions for different industries, should be watchful for this trend to grab a market share.
Market Challenges
The global refractory bricks market possesses the inherent property of heat resistance to up to 3000 degrees Celsius and above. These are used in industrial manufacturing process of steel making, glass production, and also cement production. Though creating refractory materials that will endure the structural integrity and remain functional in such impressive conditions is the main problem of intensive use of the refractory materials by producers. The refractory bricks are easily exposed to the corrosive environments which contain dioxides, chemicals, blends of metals melted together, slags, and of course the abrasive materials that are hard to smash. Refractoriness of the material against chemical corrosion and erosion is one of the main ingredients for their lasting life and attributes. Therefore, designers and engineers have a tough job. Successive thermal shocks – a phenomenon where refractory bricks undergo temperatures swings – often lead to cracking or premature failures. A high level of thermal shock resistance is mainly about design materials that are for example resistant to sudden temperature changes, just such as it is the case in kilns and furnaces.
Market Opportunities
The steel industry is one of the biggest customers of refractory bricks that are used in furnaces, ladles and another high-temperature equipment. The augmenting demand for steel products globally, intensely in industrializing countries, results in a corresponding increase in refractory need, which contributes with the market development. Refractory bricks are also used in several major industries such as cement, glass, ceramics, and non-ferrous metals stabilizing the groundwork in the development of infrastructure. Along with attempts at constructing infrastructure through roads, bridges and buildings, there is also a continuous demand for refractory materials to cater for processes such as building and making, and this creates windows for the suppliers. Manufacturing is not limited to the petrochemical, energy production and aerospace industry, rising in the need for materials that can endure extremes of high temperatures and rough conditions. The superior ability of refractor bricks to withstand the temperatures, the erosion factor and the corrosion needs no explanation when considering these in applications. Growth of these industries is proportional to the market expansion of the refractory materials, which have become more advanced.
Regulatory Factors
Quality standards and certification criteria/requirements for refractory bricks are set by regulatory bodies and industrial organizations. These minimize the vulnerability, the durability and safety of refractory bricks. Manufacturers have to comply with these standards and obtain a certification or two to convey that their products are reliable and of high quality. Shared standards such as ISO 9001 (Quality Management Systems), ASTM International (Test Methods Standard and Material Specification), and ASTM. The compositions of refractory materials may require the use of chemicals that could be classified under the discharge control regulations for such products including production, use, labeling, and disposal. Regulatory systems such as the REACH authority in the European Union and the TSCA act in the United States go through process and assessment of risk and management of chemical substances to mitigate effects on human health and the environment.
Competitive Landscape
The global refractory bricks market is highly competitive with major key players such as Vesuvius plc, RHI Magnesita, Colonial Manufacturing, and Darley Firebrick (United States). The refractory bricks market is a highly competitive market where players compete in several ways to gain and maintain market positions. Quality and performance are the main separating lines in 3-D printing technology, as companies tend to find new bricks that can withstand high temperatures, have high longer life, and also can resist wear and tear. Sustainability of materials used, and process innovation are very important, and as an added advantage, one must note the cost-efficiency as a way of offering competitive prices but without compromising on quality.