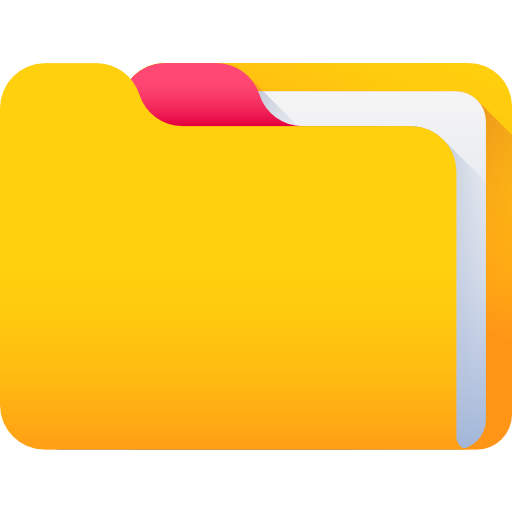
Global Honeycomb Sandwich Material Market
Pages:
197
Date:
28-06-2024
Industry:
Food and Beverages
Global Honeycomb Sandwich Material Market is a lightweight and significant structure of composite layup in which the two thin and strong face sheets are bonded with core material honeycomb, and typically aluminum, Nomex or fiberglass used for the core. The honeycomb matrix consisting of a hexagonal structure gives the highest resistance to deformation while also maintaining a low mass, making it ideal for those applications where decreasing the weight of the structure does not compromise the structural integrity. The hexagonal configuration intercepts all the loads evenly, ensuring impressive durability against bending, compression, and shear forces at the same time. Such multifaceted nature of the materials gives impetus for their use in aerospace, automotive, marine engineering, and construction fields where all are applied for the manufacturing of aircraft panels, car body panels, and hulls of boats.
North America and Europe have been the largest market for honeycomb sandwich materials ever. These regions are popular for some of the largest aerospace, automotive, and marine industrial giants with advanced composite materials such as honeycomb sandwich structures as major consumers. These centers are the growth drivers of R&D and manufacturing and as a result, secure a lead in the market.
Player Names
- 3A Composites GmbH (Switzerland)
- ACP Composites Inc. (United Staes)
- Advanced Honeycomb Technologies Corp. (United Staes)
- Argosy International Inc. (United Staes)
- Corex Honeycomb (United Kingdom)
- EconCore N.V. (Belgium)
- Euro-Composites S.A. (Luxembourg)
- Gurit Holding AG (Switzerland)
- Hexcel Corporation (United Staes)
- Honylite (India)
- Plascore, Inc. (United Staes)
- The Gill Corporation (United Staes)
- Toray Industries, Inc. (Japan)
- Tubus Bauer GmbH & Co. KG (Germany)
- Yantai Wanhua Polyurethanes Co., Ltd. (China)
Segment Analysis
1. By Material
- Aluminum
- Steel
- Composites
- Titanium
- Inconel
- Others
2. By Coating
- Untreated
- Painted
- Anodized
- Others
3. By Application
- Aerospace
- Automotive
- Marine
- Locomotive
- Construction
- Others
Market Drivers
The aerospace and defense sector, the largest contributor to the honeycomb sandwich materials, plays a prominent role. Honeycombs are a keynote in the list of preferred materials for both aircraft and spacecraft manufacturers since these maximize fuel efficiency and payload capacity. Thus, all are very promising. The automotive industry finding a way to emit less carbon requires lightweight components of honeycomb structure to cut down weight and thus enhances fuel economy. Honeycomb sandwiches enjoy wide usage in the renewable energy sector living in the wind turbine blades and solar panels. specifically, lightweight feature of them permits effective energy generation and easier transportation and installation overall.
Market Trends
Honeycomb structure substances are finding uses in renewable energy industry constructions such as wind generator blades and solar panels. These materials offer the best of structural strength while being lighter in weight which is a prerequisite for putting up support structures in renewable energy installations. Environmental factors are reaching maximum all over the industries which have encouraged the use of sustainable materials. Honeycomb sandwich materials in huge demand for its green nature, tend to be produced from recyclable materials such as metal alloys. Manufacturers are devising new methods to enhance the sustainability of materials, both their product life and beyond. Honeycomb sandwich materials is now widely used outside aerospace and road vehicles industries due to their lightweight. These are used in several sectors, such as construction, marine, and transportation, due to their high strength-to-weight ratio. As the applications of the technology expand and new innovations keep emerging, it is foreseen that the market range will keep growing.
Market Challenges
Honeycomb sandwich constructions often are more expensive than conventional materials used e.g. Aluminum and steel. The production process which uses innovative techniques such as placements and curing can result in increased total cost. Employment first and foremost of the majority of components of the honeycomb core, including Nomex, aluminum, as well as composite materials tends to be one of the main difficulties we face. The sustainability of supply chain is compromised by the dependency on some individual suppliers that are probably not consistent. The fabrication process of the sandwich parts is carried out utilizing accurate techniques by using adhesives, curing and cutting parts. These causes of difficulty are added due to high demand for the uniformity of cell size, adhesion distribution as well as overall structural strength in the manufacturing process, which leads to increased production costs and also potential defect of the product.
Market Opportunities
The honeycomb sandwiches materials can bear water and corrosive attack which enables them to be applied in a marine application which are frequently exposed to severe environments, that is, high salt contents. In marine construction, the use of special materials such as fiberglass, carbon fiber and polyurethane enable engineers to develop lightweight vessels and marine structures with high strength. From sports boats to yachts, the use of honeycomb material in sandwich panels is not only a weight saver but also an important factor that leads to the development in performance, speed, and fuel efficiency. In building, these materials have a positive effect on the energy consumption making a design lighter and prevent overload of the base supporting elements of the construction. The honeycomb sandwich structure of honeycomb spacers makes possible unique shapes in architectural designs and the stability at the same time. The success of green architecture is greatly enhanced by the high lighting of lightweight and recyclable nature of these materials which is an integral part of sustainable construction practices. The wind energy sectors opt for the use of honeycomb sandwich materials in the making of turbine blades, which require some lightweight but very strong materials for the production of whole blade and therefore minimize power lost. Being incorporated into the construction of the lightweight reinforcements for solar panels, these materials help reduce the size, thus, fostering the efficient distribution of solar power stations.
Regulatory Factors
Standards include ISO 9001 (quality management) and ISO 14001 (environmental management) firms operating as HSSP adapt to ensure compliance with quality standards and a set of prescript requirements. The speciation of certain rules for example, REACH (Registration, Evaluation, Authorization, and Restriction of Chemicals) governs the use of chemicals in honey-comb sandwich materials sold in the European Union.
Competitive Landscape
The Global Honeycomb Sandwich Material Market is highly competitive and fragmented with major key players such as ACP Composites Inc., Advanced Honeycomb Technologies Corp., Argosy International Inc., Corex Honeycomb, EconCore N.V., Euro-Composites S.A., Gurit Holding AG are Competitors in the honeycomb sandwich materials industry share various areas on which all compete. In a nut shell, performance, quality and innovation are a set of key competitive factors, where improvements in material capabilities, for instance, greater strength-to-weight ratios or fire resistance, can make a difference. In this regard, cost together with quality are major variables that companies focus to achieve most affordably done services to their customers. Moreover, together with the reliability, customer service and environmental sustainability are on the other hand more and more significant in shaping people’s attitudes towards making decisions and purchasing.