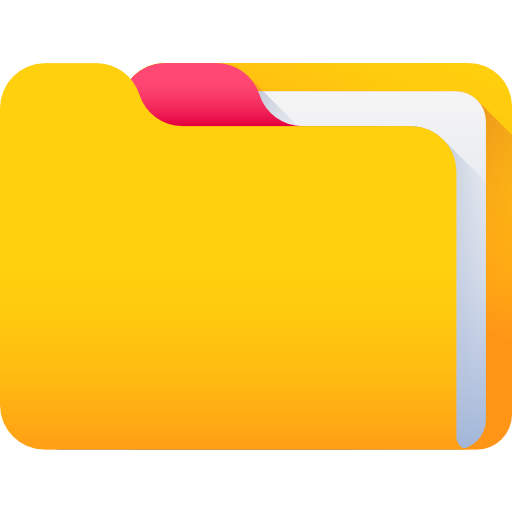
Global Aerospace Coatings Market
Pages:
223
Date:
28 June 2024
Industry:
Aerospace and Defense
Global Aerospace Coatings Market are specifically designed to be applied on surfaces of aircraft and spacecraft to achieve shielding, long-term durability, and, in some cases, even performance enhancement in aerospace conditions. These coatings constitute an integral part of the fabric of the aircraft and perform several functions, such as reducing corrosion, being a heat insulator, providing anti-icing protection, and aerodynamic optimization. These are crafted with weatherability phenomena, high altitude resistance, temperature variations, and UV/chemical exposure emission in mind along with their retention of strength and an aesthetic appearance. An aircraft finishing goes through rigorous testing to be certified with regulations and are scrutinized to achieve safety, satisfactoriness as well as environmental health and safety (EH&S). Furthermore, aerospace coating technologies remain to be the frontline feeder as the innovation in the fuel efficiency of transports, maintenance period and aircraft, performance are galaxies in improvements.
North America, especially the United States, is the region that has consistently held the first position in the international aerospace graffiti market. According to a survey, manufacturing of the aerospace sector is mainly based on the fact that the region’s major aerospace companies such as Boeing and Lockheed Martin are located there. Besides, North America has a colossal fleet of commercial and military aircraft, which generates a high interim quantity for aerospace coatings to protect and maintain those airplanes
Player Names
- 3M (United States)
- AkzoNobel Aerospace Coatings (Netherlands)
- BASF SE (Germany)
- Brycoat Inc. (United States)
- Henkel AG & Co. KGaA (Germany)
- Hentzen Coatings, Inc. (United States)
- Hohman Plating & Manufacturing, LLC (United States)
- IHI Ionbond AG (Switzerland)
- Lord Corporation (United States)
- Mankiewicz Gebr. & Co. (Germany)
- Mapaero (France)
- PPG Industries (United States)
- Sherwin-Williams Aerospace Coatings (United States)
- The Sherwin-Williams Company (United States)
- Zircotec Ltd. (United Kingdom)
Segment Analysis
1. By Type
- Polyurethanes
- Epoxy
- Polyester
- Others
2. By Technology
- Liquid Coating-based
- Solvent-based
- Water-based
- Powder Coating-based
- Others
3. By User Type
- MRO
- OEM
4. By Application
- Exterior
- Interior
5. By End User
- Commercial Aviation
- Military Aviation
- General Aviation
- Others
Market Drivers
The aviation industry is nowadays more focused on fuel efficiency and emissions reduction, so there is also an increasing demand for weight-conscious coatings that offer protection without adding unnecessary weight to the aircraft. To fulfill this need, complex coating with nano-science and composite materials makes a way by giving the best durable features while keeping lightweight tailoring. Constantly produced innovations in coating techniques originate specialized coatings that perform better than ever. all show such features as increased durability, scratch resistance, and self-healing. These technological advancements are the main reason of why airlines now try to find more reliable and cost-effective solutions and the application of aerospace coatings comes up as an option. Increasingly widespread journeys made by commercial aviation across developing regions bring an increased call for new aircraft deliveries. Due to this flight-purpose production triggers, the aerospace coating market demand receives a boost from aircraft manufacturers. The coatings are needed for both exterior and interior applications to keep the aircraft surface from corrosion, abrasion and wear.
Market Trends
Global Aerospace Coatings Market are constantly improving with the coming-up of advanced technologies such as nano-coatings, self-healing aerospace coatings and multifunctional aerospace coatings. These techniques extend the life of the part, prevent corrosion of the metal language, and manage thermal issues squeezing into space availability, which are the basic rules in the aerospace business. Now, there is a critical need for manufacture of aerospace coatings that are by the environmental laws and eco-friendly goal. Water based coating, low-VOC (volume-based organic compounds) making alternatives to the traditional solvent-based coatings is gaining popularity due to environmental consideration and health concerns. Fuel efficiency and weight reduction being two of the primary factors for the manufacturers of aerospace coating, therefore lightweight coatings are more in demand. The highly-strength-to-weight ratio coatings are envisioned to protect challenging conditions without excessive weight being added to the structure and as a result will lead to both fuel savings and improved performance.
Market Challenges
Aerospace paint systems have stringent prescriptions and specifications to guarantee the safety and durability of aerospace components as well as to address environmental issues. Addressing these demands sometimes turns into a full-fledged process of testing, certifications, and continuous rechecking for manufacturing companies, which probably takes more time and money and leads to complexity. The environmental awareness and the regulations regarding volatile organic compounds (VOCs) and hazardous air pollutants (HAPs) present new obstacles for the manufacturers of aerospace coating during which perspectives should be broadened to focus upon environmental protection rather than impermissible loss of materials. However, the research and development effort towards the formulations of low-VOC or environmentally friendly coating maintaining the performance measures might need financial strengthening. Aerospace coatings must pass industrial testing to tackle the array of extreme conditions it will encounter, such as temperature variations, high altitude, abrasion and corrosive environments. While these two conditions are currently interlinked, the circumstances could turn against one another at any moment with new technologies invariably coming on stream, the technical problems raised for manufacturers are minute at this stage.
Market Opportunities
The aviation industry is coping with a wave of aircraft orders and deliveries which are triggered by the rise in air travel demand, as well as fleets renewing their fleet and updating their aircraft. This tendency creates a huge chance for aluminum coating manufacturers since in the process of building one new aircraft a lot of coatings are needed to protect the object from corrosion, UV rays and other impacts. The growing market share of the aerospace industry in developing markets of Asia-Pacific and Middle East could be a promising factor for the companies of the aerospace coating to get new contracts. Fast-developing air transport markets in these areas are very strong together with the need for paints which are used for both civil and military purposes. The field for coatings fabricators is open for contribution to stringent environmental regulations and sustainability initiatives in the aerospace industry with the use of green products that emit lower VOC and are also environmentally friendly. Companies that give coatings compliant with the regulations and with exceptional performance and durability get a competitive edge. Similarly, to quick-serve and fast-food restaurants, retail stores rely on disposable and convenient options such as wrappers, cups, bags, and utensils. These products were designed to be used once and discarded, leading to waste buildup and environmental challenges.
Regulatory Factors
In the European countries, the EASA formulates rules and practices for aerospace coatings to enhance uniformity of the rules and systems among the member states. To get the aircraft certified and for it to carry out operations within the European Union, it is imperative to adhere to EASA rules and regulations. An Aerospace manufacturer and supplier must implement and subsequently comply with the global quality standards as identified in AS9100. These standards are designed to ensure that industry best practices and regulatory requirements are followed. These requirements are a set of guidelines for aerospace paints production covering design, manufacturing, and quality control. In the United States the TSCA is the managing organization that regulate the manufacturing, importation, use and disposal of chemical substances as well as the coatings used in aerospace. Manufacturers must follow the TSCA protocols and submit chemical notifications, conduct testing and implement risk management measures to avoid public health and environmental issues.
Competitive Landscape
The Global Aerospace Coating Market is competitive with major key players such as BASF SE, Brycoat Inc., Henkel AG & Co. KGaA, Hentzen Coatings, Inc., and Hohman Plating & Manufacturing, LLC. The leading players in aerospace coatings market positioning themselves on the basis of quality, performance, technical innovations, customer service, and global footprint. These hold state-of-art coatings solutions as studies that provide superior protection against corrosion, abrasion and environmental factors along with providing aircraft performance and fuel efficiency enhancement.’ Innovation in coating formulation and application techniques is detrimental for the development of coating and paints industry due to the fact of achieving advanced industry norms and meeting environmental set requirements. Moreover, the provision of prompt customer care, their technological support as well as the reliability of delivery chain, is undeniably paramount to remain competitive.